Improving Efficiency and Safety in Fluid and Gas Transfer Applications
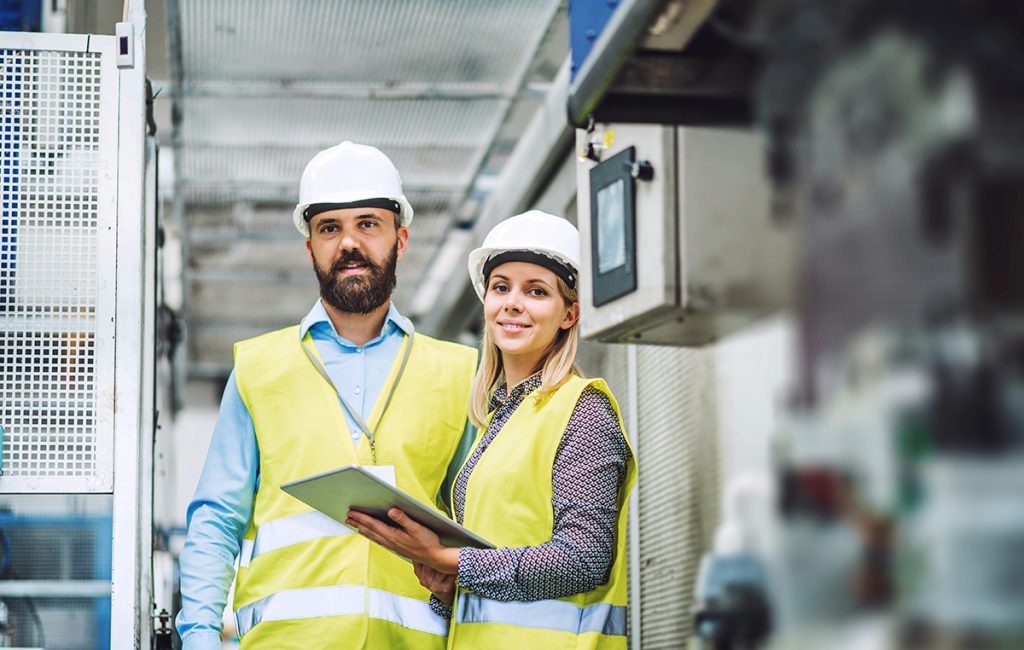
When you’re dealing with fluid transfer systems—water, oil, thermal fluid or natural gas—performance and safety aren’t goals. They’re necessities.
From swivel joints and rotary unions to complete fluid transfer equipment, selecting the right components is key to reliable operation. This guide supports better decision-making, helping engineers, maintenance teams, and system designers reduce downtime, improve performance, and maintain safe, consistent operations across a wide range of industrial applications. The focus is on improving efficiency and safety in fluid and gas transfer applications, without overcomplicating the process.
1. Choose Equipment That Matches Your Application
Not all components are created equal. Using the wrong joint or seal in a fluid transfer operation can lead to leaks, wear or worse—unplanned downtime.
When selecting the right equipment consider:
-
Chemical composition of the media
-
Boiling points and operating temperature ranges
-
Flow rates and pressure testing standards
-
Compatibility with heat transfer fluids
-
Handling and contamination requirements
Matching materials and seals to the application is the first step in improving both system efficiency and operator safety.
2. Design with Efficiency in Mind
Efficiency isn’t just about speed—it’s about high efficiency transfer with low energy use, low operational costs and fewer points of failure.
To optimise performance:
-
Keep line routing clean and direct
-
Use swivel joints to reduce hose stress
-
Choose fluid transfer technology for high performance environments
-
Prioritise precise temperature control when working with heat transfer or thermal fluid applications
A system designed for performance is safer and more cost effective in the long run.
3. Integrate with Control and Automation Systems
Smart systems are safe systems. Integrating automation and control systems—especially those with PLCs and safety functions—provides real-time monitoring, early fault detection and automatic shutdown if thresholds are exceeded.
This kind of system integration is especially important in industries like power generation, chemical processing or tanker loading where small faults can have big consequences.
4. Think About Maintenance from the Start
All systems require maintenance. Designing with maintenance in mind makes maintenance faster, safer and cheaper in the long run.
Must haves include:
-
Easy access to seals and bearings
-
Modular or replaceable components
-
Documentation to manufacturer’s standards
-
Built in pressure test ports and clean out access points
This keeps the system running longer and minimises downtime.
5. Reduce Risk in Hazardous Applications
Transferring bulk liquids, crude oil or sulphur dioxide requires designs that meet strict safety standards for operator safety and environmental protection.
Must haves include:
-
Ventilation and safe handling protocols
-
Components designed for high pressure
-
Flow paths that prevent chemical reactions
-
Isolation points to prevent contamination
Safety, performance and environmental impact are all determined in the early stages of design.
6. Tailor Your System to Industrial Needs
Every industrial process is different. Customised design is far better than a one size fits all.
Across various industries from chemical manufacturing to power generation tailored systems deliver better transfer and longer life.
Key areas to focus on are:
-
Storage tanks and line routing
-
Smart flow control with technology
-
Cost effective while meeting safety goals
-
Working with manufacturers that meet sector standards
Don’t forget the detail when transferring hazardous or high value media.
Design Mistakes to Avoid
Don’t wait for major problems later. Frequent mistakes:
-
Using seals not compatible with the process media
-
Ignoring thermal expansion in pipe layouts
-
Not testing pressure before commissioning
-
Too many bends or joints in flow paths
-
General purpose components instead of application specific ones
Planning reduces risk and costs of retrofits.
Checklist: What to Consider in Your Fluid & Gas Transfer Design
Before finalising a system run through this checklist. Is the equipment rated for the chemical composition and temperature range of your media? Are flow rates and pressures controlled? Are safety features for operators included? Is maintenance access easy? Does it connect to your automation and control systems? And are industry standards and regulations followed?
Answering these questions up front means a safer and better outcome.
What’s the Long-Term Value?
Purpose built components may cost more upfront but the ROI is clear over time:
-
Longer life for all system components
-
Less emergency repairs and unplanned downtime
-
More energy efficiency and lower operating costs
-
Better day to day performance
-
Higher throughput and system availability
A well thought out investment now means long term operational and financial benefits.
Need Help Reviewing or Planning a System?
Designing or upgrading a fluid or gas transfer system can be tricky, especially when safety, compliance or high performance is involved.
Key areas to consider:
-
Review current setup to identify risks or inefficiencies
-
Choose components to the application, media and conditions
-
Advise on layout, routing and system architecture
-
Check compatibility, flow rates and pressure requirements
Good guidance during the design process makes for better outcomes and less project risk.
Frequently Asked Questions
What’s the difference between a swivel joint and a rotary union?
A swivel joint is single axis rotation and used in hose assemblies. A rotary union transfers fluid across rotating parts and is for continuous or multi directional rotation.
Can the same swivel joint be used for different media types?
Only if the seals and internal materials are compatible with each fluid or gas involved. Matching components to the media is key.
What causes systems to fail early?
Incorrect material selection and not accounting for thermal expansion is common. Early stage planning is key to long term performance.
How often should pressure testing be done?
Before first use and at intervals determined by operating conditions, especially in high pressure or hazardous systems.
Is help available with component selection?
Yes. Many suppliers and consultants offer specification support to system requirements and performance goals.
Final Summary
Building a safe, efficient fluid or gas transfer system is more than just assembling parts – it’s planning, selecting the right components and focus on long term performance. By considering media compatibility, pressure control, operator safety and system maintainability, engineers can create solutions that deliver results.
For those looking for trusted expertise and high quality components, Sreg Products design and supply swivel joints, swivel joint systems and multi-port rotary unions – we’re the kind of engineering that gets it right first time.
Take the time to review your current setup, ask the right questions and invest in performance that lasts.